Business
Pallet Racking Audits: Ensuring Safety and Efficiency
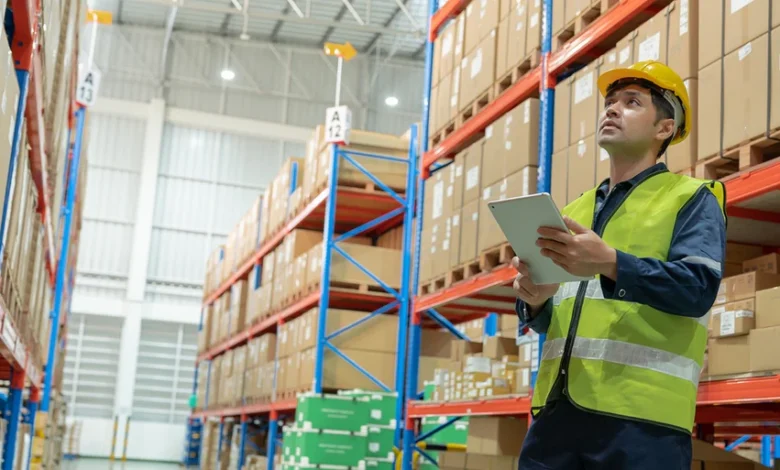
Pallet racking systems are essential for efficient warehouse operations, but they also pose significant safety risks if not maintained properly. Regular pallet racking audits are crucial to identify potential hazards, ensure compliance with safety regulations, and optimize storage capacity.
Why Conduct Pallet Racking Audits?
- Safety: Regular inspections can identify potential hazards like damaged beams, bent columns, or loose components, preventing accidents and injuries.
- Compliance: Adhering to local and national safety regulations is mandatory. Audits ensure compliance and avoid costly penalties.
- Efficiency: A well-maintained racking system optimizes storage space and improves order picking efficiency.
- Cost-Effectiveness: Identifying and addressing issues early on can prevent costly repairs and downtime.
- Insurance Requirements: Many insurance policies require regular inspections to maintain coverage.
Key Areas to Inspect During an Audit
- Structural Integrity:
- Columns: Check for damage, corrosion, and misalignment.
- Beams: Inspect for bending, cracking, or excessive wear and tear.
- Bracing: Verify the integrity of horizontal and diagonal bracing.
- Bolts and Nuts: Ensure they are tight and secure.
- Load Capacity:
- Pallet Weight: Verify that the weight of stored pallets does not exceed the rated capacity of the racking system.
- Load Distribution: Ensure pallets are evenly distributed on beams to avoid overloading.
- Floor Conditions:
- Levelness: Check for uneven floors, which can impact the stability of the racking system.
- Damage: Inspect for cracks, holes, or other damage that could compromise the floor’s load-bearing capacity.
- Forklift Traffic:
- Damage: Look for damage caused by forklift impacts, such as bent columns or damaged beams.
- Traffic Patterns: Ensure forklift traffic is properly directed and controlled.
- Corrosion:
- Rust: Inspect for rust on metal components, especially in areas with high humidity.
- Corrosion Protection: Verify that corrosion protection measures are in place, such as painting or galvanizing.
- Maintenance Records:
- Documentation: Review maintenance records to track repairs, inspections, and modifications.
Best Practices for Pallet Racking Audits
- Regular Inspections: Conduct regular inspections, ideally every 12 months, or more frequently in high-traffic or harsh environments.
- Qualified Inspectors: Ensure that inspections are performed by qualified personnel with knowledge of racking systems and safety regulations.
- Detailed Documentation: Maintain detailed records of inspection findings, including photographs and measurements.
- Corrective Action Plans: Develop and implement corrective action plans to address identified issues promptly.
- Training: Train warehouse staff on safe racking practices, including proper loading and unloading techniques.
- Emergency Procedures: Have emergency procedures in place for incidents involving pallet racking, such as evacuations and damage control.
By prioritizing pallet racking audits, businesses can create a safer, more efficient, and compliant warehouse environment. Remember, a well-maintained racking system is not only a safety asset but also a significant contributor to operational success.