Innovations in Commercial Sieving Technology for Modern Industries
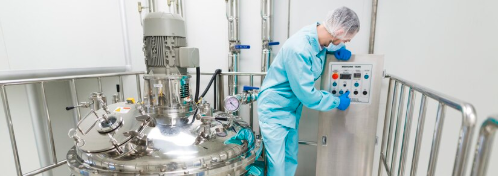
Introduction
Centrifugal solid-liquid separators play a crucial role in industries such as food processing, pharmaceuticals, wastewater treatment, and chemical manufacturing. They use centrifugal force to separate solid particles from liquids, ensuring cleaner fluid streams and more efficient operations. However, achieving optimal performance requires proper setup, maintenance, and operational strategies.
This guide explores key methods to improve the efficiency of your centrifugal solid-liquid separator, reducing downtime, increasing throughput, and lowering operational costs.
Understanding Centrifugal Solid-Liquid Separation Efficiency
What Determines Efficiency?
The efficiency of a centrifugal separator depends on several factors, including particle size and density, flow rate, separation chamber design, and rotational speed. Larger and denser particles separate more easily than smaller, lighter ones.
Centrifuge solid-liquid separation provides highly efficient separation by using centrifugal force to rapidly isolate solids from liquids. This results in improved product purity, reduced processing time, and lower operational costs, making it ideal for industries like pharmaceuticals, food processing, and wastewater treatment.
An optimal flow rate ensures effective separation without overwhelming the system. The shape and size of the separation chamber influence the separation process, while higher rotational speeds generate stronger centrifugal forces, improving separation but also increasing energy consumption.
See also: Tech Troubles? How To Know When Your Business Needs Professional IT Support
Key Ways to Improve Efficiency
Optimize Flow Rate for Maximum Performance
Flow rate is a critical factor affecting separation efficiency. Too high of a flow rate can cause incomplete separation, while too low of a rate can lead to unnecessary energy consumption. Adjusting the flow rate according to manufacturer recommendations, using flow control valves, and monitoring throughput capacity can enhance performance.
Increase Rotational Speed Carefully
The speed of the centrifugal separator directly impacts its efficiency. However, excessive speed can lead to wear and tear, increasing maintenance costs. Gradually increasing rotational speed while monitoring separation efficiency, ensuring the separator’s materials and design can withstand higher speeds, and using a variable speed drive (VSD) can optimize performance.
Improve Separation Chamber Design
A well-designed separation chamber ensures optimal distribution of centrifugal forces and maximized efficiency. Upgrading to a multi-stage separator can improve fine particle separation, while optimizing chamber shape and size based on the type of material being processed enhances performance. Ensuring even distribution of materials within the chamber prevents turbulence and inefficiency.
Utilize Pre-Filtration Methods
Pre-filtration can remove larger particles before they enter the centrifugal separator, reducing the load and improving efficiency. Using mesh screens or settling tanks, employing hydrocyclones or sedimentation filters, and reducing contaminant loads help prevent excessive wear on the separator.
Optimize Energy Consumption
Reducing energy usage while maintaining performance leads to cost savings and improved efficiency. Investing in energy-efficient motors, using automatic load sensors to adjust power usage, and regularly monitoring energy consumption help optimize operational efficiency.
Implement Automation and Monitoring Systems
Modern centrifugal separators can be integrated with automation technologies to enhance efficiency and performance. Real-time monitoring sensors track flow rates, particle separation efficiency, and wear levels. Automated speed adjustments match changing material conditions, while predictive maintenance systems detect issues before they cause failures.
Troubleshooting Common Efficiency Issues
Low Separation Efficiency
Low efficiency may result from incorrect flow rate or speed settings, excessive buildup of solids in the chamber, or inadequate particle size distribution. Adjusting flow rate and rotational speed, increasing maintenance frequency to prevent blockages, and using pre-filtration techniques can improve performance.
Excessive Wear and Tear
High operating speeds, poor lubrication of moving parts, and abrasive materials can cause excessive wear and tear. Using wear-resistant materials for high-stress components, maintaining proper lubrication schedules, and reducing excessive operating speeds help extend equipment life.
Clogging or Blockages
Clogging may occur due to improper nozzle size, accumulation of fine particles within the chamber, or inadequate discharge mechanisms. Adjusting nozzle size, increasing cleaning frequency, and utilizing automatic purging systems prevent blockages and ensure continuous operation.
Conclusion
Improving the efficiency of your centrifugal solid-liquid separator requires proper equipment selection, regular maintenance, optimized flow rates, and energy-saving strategies. Fine-tuning operational settings, utilizing pre-filtration methods, and leveraging automation can achieve higher productivity, reduced downtime, and significant cost savings. Investing in these efficiency-boosting techniques enhances performance and extends the lifespan of your separator, ensuring maximum return on investment.